UTILIZATION IN MEDIUM SIZE (200 KW-1 MW) BOILERS
Fortum Oil & Gas (presently Neste Oil) has been developing combustion
related equipment for the past several years together with Oilon OY
of Finland.
In the project, the equipment developed by Oilon has been utilized
without further modifications. It was found that in order to achieve
clean combustion, a special burner retention head is required. This
is because pyrolysis liquids which contain significant amounts of
water have much lower heating value than hydrocarbon oils. This means
that the amount of air to combust the pyrolysis liquid is approximately
half compared to conventional fuels. A burner head was developed by
Oilon taking this into consideration. In addition, the control system
and the pump were changed.
The main aim of the performed tests has been to assess the technical
feasibility of the designed combustion system during long duration
tests of pyrolysis liquid. Special attention has been paid to material
durability and deposit formation in valves, heaters, nozzles, burner
retention heads and on boiler walls and to check the changes in the
emission levels.
Different grades of pyrolysis oils were tested. Forestera™
produced from wood chips, having a solid content varying from 0.1
wt% to 0.04 wt% and water content 22-26 wt%, was tested.
Field trials were carried out in a heating oil boiler in Saarijärvi
at the Thermia Oy plant. A total of more than 12000 liters of Forestera™
was combusted of which 4000 litres were for the COMBIO project and
the boiler ran more than 1500 on-off cycles giving valuable feedback
to further process improvements.
Start up and shut down operations were run with light fuel oil and
the system was totally automated with the boiler being under the control
of a thermostat.
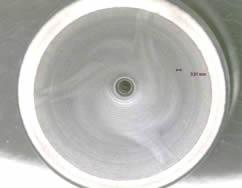
erosion in nozzle |
Early tests pointed out the importance of achieving very low levels
of solids in the fuel. This resulted by both high levels of emissions
and by erosion in the nozzles. Further development at the pilot plant
reduced the solid levels to values <0.05 wt% which gave the emission
levels presented in the table below.
It was found in these field trials that any inclusion of sand or
any other hard solid in the liquid would cause erosion in the pump
and in the nozzles. Nozzles had to be replaced every 1000 litres of
fuel combusted. Emissions were also effected with higher particulates
found in the flue gas. The erosion is due to the high pressure, 17-20
bar, required to obtain small drop size and clean combustion.
The emissions from the prototype burner in the Saarijärvi boiler
were very low, approaching those of a light fuel oil boiler:
CO |
30 ppm |
O2 |
4,5 % |
Particulate |
no organic, only ash |
The tests were run with pyrolysis oil having a solid content reduced
by centrifuging to a value lower than 0.05 weight % and the nozzles
showed no signs of erosion.
Technically the combustion system was a success and could be used
for long term heat production. The cost of the combustion system was
however higher than conventional systems due mainly to the cost for
the industrial pump required but also to the increased automation.